In den letzten Jahren kam es immer häufiger zu Bränden in Galvanisieranlagen, die zu schwerwiegenden Schäden führten. Beispielhaft steht dafür ein Brand in der Galvanik eines Zulieferers für die Flugzeugindustrie, bei dem Ende 2018 ein Millionenschaden im zweistelligen Bereich entstand. Es wird erwartet, dass die Galvanikabteilung für mindestens ein Jahr ausfällt. Aufgrund eines vorhandenen Notfallmanagements sowie der Möglichkeit, die Oberflächenbearbeitung an andere Standorte auszulagern, geht der Zulieferer zunächst davon aus, keine nennenswerten Lieferverzögerungen zu erleiden.1
Neben dem materiellen Schaden durch Feuer und Explosionen verursachen Löschwasser und austretende Chemikalien Umweltschäden. In Kombination mit den sich daraus ergebenden Betriebsunterbrechungen führen die Brände zu erheblichen Schäden für die Versicherer.
Die Galvanotechnik ist in der Oberflächen- und Schichttechnik ein Überbegriff und beinhaltet im eigentlichen Sinne die elektrochemischen, im erweiterten Sinne jedoch auch die chemischen Verfahren der Metallabscheidung und Umwandlung von Metalloberflächen mithilfe chemischer Reduktionspartner aus wässrigen Metallsalzlösungen, inklusive der Vor- und Nachbehandlung.
Definition
Unter Galvanisieren (auch unter den Begriffen Galvanotechnik, Elektroplattieren bekannt) wird u. a. die elektrochemische Abscheidung von metallischen Schichten auf einem Gegenstand verstanden. Dabei wird durch ein elektrolytisches Bad Strom geleitet. Das Metall, das als Schutzschicht auf dem Werkstück aufgebracht werden soll, stellt den Pluspol (Anode) dar; das zu beschichtende Werkstück wird an den Minuspol (Kathode) der Gleichstromquelle angeschlossen.
Zu erwähnen ist, dass die Galvanotechnik weitere Verfahren umfasst, u. a. auch chemisches Galvanisieren, Band-/ Trommelgalvanisieren und Chromatieren.
Das Plattierungsmetall kann entweder auf leitende (aus Metall) oder nicht leitende Oberflächen (z. B. Plastik, Holz, Leder) übertragen werden. Letztere müssen durch eine Vorbehandlung mit organischen Verbindungen oder wässrige Lösungen leitfähig gemacht werden. Hierbei werden zum Teil Stoffe wie Aceton mit einem Flammpunkt von -20 Grad Celcius eingesetzt.
Dank des Galvanisierens können Hersteller weniger kostenintensive Materialien wie Stahl oder Kunststoffe für die Herstellung ihrer Produkte verwenden, die dann im Rahmen des Galvanisierungsprozesses durch das Aufbringen einer Metallschutzschicht veredelt werden, mit dem Ziel,
- dem Produkt ein hochwertigeres/dekorativeres Erscheinungsbild zu verleihen,
- spezielle Oberflächeneigenschaften zu erzielen (z. B. Beständigkeit gegen Korrosion und Abnutzung),
- dem Produkt erweiterte technische oder mechanische Eigenschaften zu verleihen (z. B. eine höhere Verschleißwiderstandsfähigkeit, Verbesserung der elektrischen Leitfähigkeit).
Die Galvanotechnik ist in der herstellenden Industrie weitverbreitet, z. B. in der Automobil-, Flugzeug-, Elektronik-, Schmuck- und Spielwarenindustrie.
Prozess
In der Galvanotechnik sind die verschiedensten Anlagen in den unterschiedlichsten Größen und Anwendungsbereichen zu finden. Die Größe der Anlagen variiert je nach der Dimension der zu beschichtenden Werkstücke, hängt aber auch vom Verfahrensprozess und der Stückzahl ab. So gibt es beispielsweise Kleinanlagen mit Wannenvolumina von lediglich einigen Litern und Großanlagen mit mehr als 100 m³ Wannenvolumina.
Insgesamt lassen sich drei grundsätzliche Verfahrensschritte im Rahmen der Galvanotechnik unterscheiden:
- Vorbehandlung
- Galvanisierung
- Nachbehandlung
Um die Beschichtung des Werkstücks zu vereinfachen bzw. überhaupt erst zu ermöglichen, wird das Werkstück in aller Regel vor dem eigentlichen Galvanisieren vorbehandelt. Die häufigsten Methoden sind:
- Entfetten: Durch fettlösende Chemikalien (oft eine wässrige Kochsalzlösung mit Tensiden) oder durch einen elektrolytischen Prozess werden Fette und Oxide von der Oberfläche entfernt. Bei Letzterem erzeugt die elektrochemische Reaktion Wasserstoff und Sauerstoff.
- Beizen: Hierbei wird das Werkstück in Bäder getaucht, die sowohl die Oberfläche reinigen als auch Oxidschichten entfernen. Ob dafür eine saure oder eine alkalische Lösung verwendet wird, hängt von dem verwendeten Werkstückmaterial ab.
- Physikalische Reinigung: Durch mechanische Energie wie Polieren, Abstrahlen, Schleifen, Abbürsten oder Ultraschallagitation werden Kontaminierungen von der Oberfläche des zu plattierenden Gegenstands entfernt.
Im nächsten Schritt der Galvanisierung wird bei der elektrochemischen Behandlung durch ein elektrolytisches Bad Gleichstrom geleitet. Der Pluspol (Anode) besteht dabei aus dem Metall, das aufgebracht werden soll, die Kathode (Minuspol) aus dem zu beschichtenden Werkstück. Dabei löst der elektrische Strom Ionen aus dem Beschichtungsmetall ab, die sich am Werkstück anlagern, wodurch dieses dann gleichmäßig mit einer Metallschicht überzogen wird. Je länger das Werkstück im Bad verbleibt und je höher der elektrische Strom, umso dicker ist die aufgetragene Metallschicht. Je nach den Merkmalen der erforderlichen Beschichtung werden verschiedene Elektrolyte verwendet (z. B. auf der Basis von Aluminium, Chrom, Kupfer, Nickel, Zink). Die Elektrolyte befinden sich in der Regel in speziellen gegen Korrosion geschützten Wannen; in der Regel findet man Wannen aus Kunststoff vor.
Je nach gewünschtem Ergebnis kann eine breite Palette an Metallen für das Galvanisieren verwendet werden – z. B. Zink für eine Schutzschicht; Kupfer, Nickel, Chrom, Zink und Zinn für eine dekorative Beschichtung; Gold, Silber, Platin, Zinn, Blei, Ruthenium, Rhodium, Palladium, Osmium und Iridium für eine funktionale Beschichtung.
Das galvanisierte Werkstück wird häufig nachbehandelt. Hierbei handelt es sich in der Regel um einen mechanischen Prozess – beispielsweise Fetten, Ölen, elektrostatisches Ölen usw. – oder einen chemischen Prozess wie stromloses Chromatieren.
Risiken
Angesichts der verwendeten Anlagen, Prozesse und Bedingungen ist es nicht verwunderlich, dass die Galvanisierung erhebliche Risiken für Mensch, Eigentum und Umwelt birgt.
Typische Ursachen für Brände in Galvanikbetrieben sind nach Erkenntnissen der Versicherer u. a.:2
- Austrocknen elektrisch beheizter Bäder
- fehlende oder nicht funktionierende Übertemperatur- oder Füllstandsüberwachungsregler
- automatischer Anlauf der elektrischen Heizelemente ohne Medienkontakt
- zu geringer Abstand zwischen Heizelementen und Wannen aus brennbarem Material
- Überheizen der Antriebseinheiten, Kugellager oder Gleichstromversorgung, insbesondere bei nicht überwachten Prozessen in der Nacht
- Korrosion der Anschlusskontakte von Elektroden und elektrischen Verbindungen durch die hohe Luftfeuchtigkeit in Verbindung mit der zum Teil belasteten Luft/korrosiven Atmosphäre bei der Verarbeitung
- Selbstentzündung von Chemikalien
- Reinigung mit brennbaren Lösungsmitteln
- Kurzschlüsse, defekte Elektroinstallationen
- hohe Betriebstemperaturen
Zudem gibt es weitere Faktoren in Galvanikanlagen, die den Grad, in dem Brände entstehen und sich ausbreiten können, erheblich beeinflussen und damit entsprechende Schäden deutlich vergrößern:
- Ansammlung brennbarer oder explosiver Stoffe, z. B. Schmiermittel, Öle, Entfettungsmittel
- Verwendung von brennbaren Materialien, z. B. zum Polieren; Verpackungsmaterial; Kunststoffbehälter und -wannen; mit Kunststoff oder Gummi ausgekleidete Wannen; Anlagenbauteile aus brennbaren Materialien, z. B. Absaughauben und -kanäle aus Kunststoff
- Explosionsgefahr durch die Entstehung brennbarer Luft-/Wasserstoffgemische während der Galvanisierung
- Verwendung von Elektrolyt, die in Kombination mit Wasser/Löschwasser korrosiv, reaktiv und möglicherweise toxisch, wenn nicht sogar entflammbar sind
- Verwendung von brennbaren Baustoffen und Bauteilen für die Gebäude – beispielsweise Sandwich-Elemente in Außenwänden und Dächern
- unzureichende Feuerwiderstandfähigkeit tragender Bauteile, z. B. Stützen, Binder
- fehlende oder unzureichende feuerbeständige bauliche Trennung des Galvanikbereichs von angrenzenden Bereichen (z. B. Lager) oder unzureichender Schutz vorhandener Öffnungen in solchen Wänden
- unangemessene oder fehlende Installation von Branderkennungs- und Brandbekämpfungssystemen, die ggf. zu Verzögerungen in der Brandbekämpfung führen bzw. eine effektive Brandbekämpfung erschweren
- Erschwernis der Brandbekämpfung für die Löschkräfte durch
- die für die Galvanisierung verwendeten toxischen oder umweltschädlichen Stoffe, die möglicherweise mit dem Löschwasser reagieren
- Gefahren der elektrischen Energie (insbesondere Gleichspannung). In der Regel besteht aufgrund der Gleichspannung keine Personengefährdung, Problem ist jedoch, da Stromschienen in der Regel nicht isoliert verlegt werden, wenn diese durch metallische Gegenstände (Werkzeuge etc.) überbrückt werden. Aufgrund der hohen Stromstärken kann es dann zu schweren Verbrennungen kommen, da Metall schlagartig oder explosionsartig verdampft.
- ggf. notwendig werdende große Mengen an Löschwasser und Schaumkonzentrat
- begrenzt zur Verfügung stehende Einsatzmaterialien für die Löschkräfte, z. B. erforderliche Schutzkleidung, Atemschutzgeräte
Im Brandfall sind erhebliche Kontaminations- und Korrosions-Folgeschäden durch den entstehenden Brandrauch an den Gebäuden, Einrichtungen, Anlagen und Vorräten zu erwarten; die Aggressivität der Brandgase ist eine typische Begleiterscheinung dieser Betriebsart. In die Umwelt freigesetzter Brandrauch kann aber auch zu Schäden in benachbarten, vom Brand nicht direkt betroffenen Bereichen führen. Prozessbäder können durch Rauch und/oder Löschwasser kontaminiert und so unbrauchbar werden.
Des Weiteren kann es zu Umweltschäden durch das Einleiten von auslaufenden Flüssigkeiten aus beschädigten Wannen und Behältern in die Kanalisation und Fließgewässer kommen, da es sich bei den meisten für den Galvanisierungsprozess benötigten Flüssigkeiten um Säuren/Basen handelt.
Schadenstatistik
Recherchen im Internet lassen keine aussagekräftigen Ergebnisse in Bezug auf Brandschäden in Galvanikbetrieben zu. Selbst die Statistiken des Gesamtverbandes der Deutschen Versicherungswirtschaft (GDV) sind nicht eindeutig, da sich Brände nicht nur in auf die Galvanotechnik spezialisierten Unternehmen, sondern auch in zahlreichen Produktionsbetrieben mit einer Galvanikabteilung als Nebenbetrieb ereignen. Ein Schaden in einem solchen Nebenbetrieb wird aber nicht immer in den Statistiken als Galvanisierungsschaden erfasst. Daher sollten statische Aussagen mit Vorsicht betrachtet werden.
Laut einer internen Arbeitsgruppe des GDV ereignen sich in galvanotechnischen Anlagen jährlich 70 bis 80 Brände,3 10 bis 15 hiervon sind Großschäden, bei denen ein Schaden von mehr als EUR 500.000 entsteht. Die Hauptursachen (rund 70 %) liegen in der Überhitzung der Heizelemente oder elektrische Fehlfunktionen, die einen Anteil von mehr als 90 % des Gesamtschadens aller untersuchten Fälle ausmachen.
In knapp 40 % der untersuchten Schäden lagen die Ursachen in fehlenden oder defekten Vorrichtungen für eine automatische Abschaltung und/oder Füllstandsüberwachung. Solche Schäden treten häufig in Zeiten geringer Auslastung sowie Aufwärmphasen auf oder wenn nur wenige oder gar keine Mitarbeiter anwesend sind. Berichtet wurde auch, dass es durchschnittlich ca. 24 Monate dauert, bis die Galvanik wieder vollständig betriebsbereit und funktionsfähig war bzw. das Niveau der Produktionsleistung vor Eintreten des Schadens erreicht wurde. Zusätzliche behördliche Auflagen beim Wiederaufbau erschwerten in einer Reihe von Schadenfällen die schnelle Wiederaufnahme des Betriebs zusätzlich.
Bei Anlagen, die durch entsprechende automatische Feuerlöschanlagen (z. B. Sprinkleranlage) geschützt sind, ist das Schadenausmaß deutlich niedriger. Die Analyse der GDV-Arbeitsgruppe zeigte, dass der erwartete Schaden bei einem Galvanikbetrieb ohne Sprinkler sechsmal höher ist als bei einer Anlage, die durch eine adäquate Sprinkleranlage geschützt ist.4
Betrachtet man die durchschnittlichen Versicherungssummen von Galvanikbetrieben und angefallene Brandschäden, zeigen die offiziellen Statistiken des GDV für gewerbliche Risiken gewisse Schwankungen auf der Schadenseite (siehe Abbildung 1).
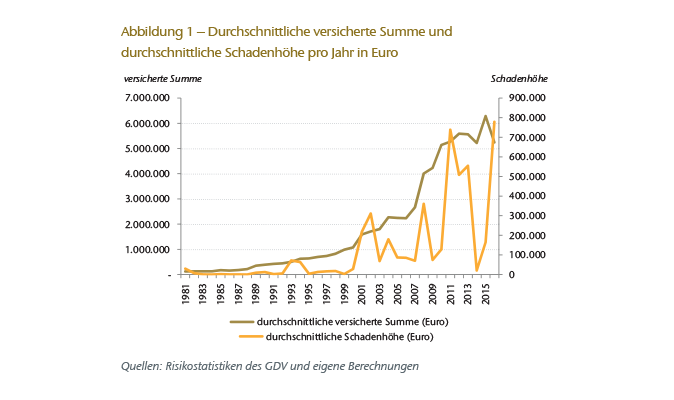
Daher schwanken Schadenbedarf und Schadenwahrscheinlichkeit stark (siehe Abbildung 2).
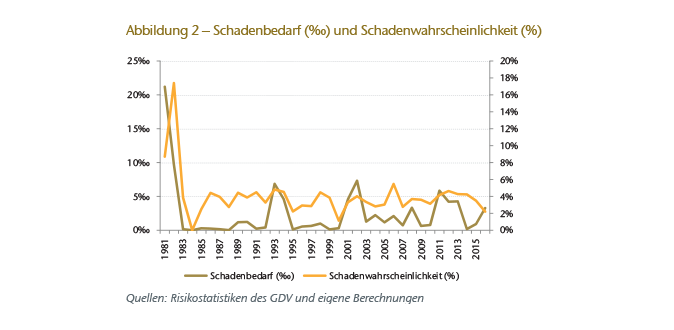
Aufgrund signifikanter Brandschäden in der jüngeren Vergangenheit mit erheblichen Betriebsunterbrechungsschäden, rücken Galvanisierungsbetriebe seit einigen Jahren immer mehr in den Fokus der Versicherer. Um dem beobachteten Schadentrend gegenzusteuern, veröffentlichte der GDV u. a. zwischenzeitlich Richtlinien für den Brandschutz bei Galvanisierbetrieben mit einer Vielzahl von Informationen zu beobachteten Schadenursachen sowie Empfehlungen, wie Brandschäden in solchen Betrieben verhindert bzw. Brandschadenfolgen verringert werden können. Eine Übersicht wesentlicher Brandschutzempfehlungen findet sich am Ende dieses Artikels.
Brandschaden
Am Samstag, den 10. März 2018, brach in der Galvanisieranlage eines deutschen Automobilzulieferers ein Brand aus. Rund 150 Feuerwehrleute und 22 Feuerwehr- und Rettungsfahrzeuge versuchten, das Feuer in dem 5.600 Quadratmeter großen Gebäude unter Kontrolle zu bringen, das mehrere bis zu 20 Kubikmeter große Becken mit hochkonzentrierter Säure und Lauge enthielt. Am Gebäude traten schwere Bauschäden auf. In den Innenhof floss Löschwasser, gemischt mit einer gefährlichen Kombination aus Lauge und Säure, und zwang die Feuerwehr zum Rückzug und zur Neuorganisation der Brandbekämpfung. Niemand wurde verletzt, aber der Schaden wird auf über 30 Mio. Euro geschätzt.5 Fünf Monate später war der Versicherte zahlungsunfähig, da die Geschäftsprozesse des Unternehmens stark beeinträchtigt waren und er seine Kunden verlor.6
Underwriting-Hinweise
Angesichts der Vielfältigkeit der einzelnen galvanotechnischen Anlagen und Prozesse und der unterschiedlichen Gefahren ist eine differenzierte Betrachtung der individuellen Risiken erforderlich.
Underwriting und Prämienfindung für Galvanisierungs-/galvanotechnische Risiken sollten stets auf einem aktuellen Besichtigungsbericht eines Versicherungsingenieurs basieren. Ist die Galvanisierung ein Nebenbetrieb eines Produktionsbetriebs, z. B. in der Schmuck-, Kunststoff- und Metallindustrie, sollte neben der Besichtigung des Hauptbetriebs ein besonderes Augenmerk auf die Galvanikabteilung gelegt werden. Hierbei identifizierte Risiken und Mängel, die zu möglichen Brandschäden führen könnten, sollten während der Besichtigung mit dem Ziel zur Sprache gebracht werden, dass sie schnellstmöglich behoben werden.
Besondere Aufmerksamkeit sollte auf den Umfang der Deckung im Versicherungsvertrag und die Richtigkeit der Versicherungssummen gelegt werden, da es bei solchen Betrieben im Laufe eines Jahres zu erheblichen Änderungen kommen kann, die zu einer Veränderung des Betriebs- und Brandrisikos und letztlich im Schadenfall auch zu einer Einschränkung des Versicherungsschutzes führen können.
Das Risiko einer Betriebsunterbrechung sollte im Rahmen der Betriebsbesichtigung und des nachfolgenden Underwriting nicht mehr nur als Anhang zur Sachversicherung angesehen werden, sondern separat berücksichtigt werden. Schäden zeigen, dass beispielsweise aufgrund der langen Lieferzeiten für die Ersatzteile, aber auch zusätzliche Auflagen lokaler Behörden beim Wiederaufbau nach einem Schadenfall der Zeitraum bis zur Wiederaufnahme des Betriebs länger sein kann als erwartet und damit eine deutliche Vergrößerung des Schadens einhergeht.
Insbesondere sollten in das Underwriting des Versicherers die folgenden Überlegungen mit einfließen:
- Eigenständige Galvanikbetriebe sind in der Regel kleine bis mittlere Betriebe, die meist aus nur einem Komplex bestehen, bei dem eine erhöhte Totalschadenwahrscheinlichkeit für den Betrieb besteht.
- Ist der Galvanikbetrieb ein Nebenbetrieb in einem größeren Unternehmen, z. B. in Betrieben der Flugzeugbau-, Kunststoff-, Elektronik- und Schmuckherstellung, geht dies oft mit einer Erhöhung des Hauptbetriebsrisikos einher, wenn ein solcher Nebenbetrieb brandschutztechnisch nicht ausreichend abgetrennt ist bzw. keine installierten technischen Brandschutzmaßnahmen aufweist, die dieses erhöhte Risiko minimieren.
- Schadenfälle zeigen immer wieder, dass sich die gemeldete Versicherungssumme im Schadenfall häufig als unzureichend herausstellt, insbesondere für angefallene Sach- und/oder Betriebsunterbrechungsschäden. Deshalb empfiehlt es sich, die Versicherungssumme regelmäßig zu prüfen und ggf. zu aktualisieren.
- Die Folgeschäden nach einem Brand werden häufig unterschätzt, da es dem betroffenen Unternehmen oft nicht möglich ist, die Produktion im notwendigen Umfang an einen anderen Standort zu verlegen oder auf Dritte auszulagern. Hinzu kommt, dass die Lieferzeit für bestimmte Ersatzteile länger ist als erwartet (bei Großschäden häufig mehr als 18 Monate), oder beispielsweise behördliche Auflagen einschließlich Zutrittsverbote erlassen werden, sodass die Lieferfähigkeit des Betriebs massiv gefährdet ist, mit der Folge, ggf. wichtige Kunden zu verlieren.
- Deckungserweiterungen in der Versicherungspolice (sog. Erstrisikopositionen), z. B. Brandbekämpfungs-, Aufräum-, Dekontaminierungskosten, Bußgelder, Kosten verursacht durch behördliche Auflagen, Mehrkosten, können den Schadenaufwand für den Versicherer weiter steigern. Dies gilt auch für eventuell vereinbarte individuelle Klauseln im Rahmen des Sachversicherungsvertrags oder aus einem Kumul mit gezeichneten Maschinenbruch-, Haftpflicht- und Umwelthaftpflichtpolicen. Daher empfiehlt sich ein genauerer Blick in den Versicherungsvertrag, um für ein vorliegendes Risiko einen Überblick über den vollständigen Umfang der Deckung zu erhalten und im Fall eines Schadens Überraschungen zu vermeiden.
- Schäden in Galvanisierungsunternehmen sind tendenziell groß. In den meisten Fällen ist ein Höchstschaden (MFL/PML) von 100 % nicht überraschend, wenn adäquate, wirksame räumliche oder bauliche Komplextrennungen fehlen.
- Sollten neben der Feuergefahr weitere Gefahren in der Versicherungspolice versichert sein, z. B. Naturgefahren wie Erdbeben und Überschwemmung, sollten diese Gefahrenerweiterungen mit in die Unterwriting-Entscheidung einbezogen werden, da auch aus diesen Gefahren Großschäden erwachsen können, z. B. Kontaminierungen der Umgebung und des Grundwassers durch z. B. Bruch/Leckage der Wannen, Rohrleitungen, Aufschwimmen/Zerstörung der Wannen.
Zusammenfassung
Galvanisierung ist ein industrieller Betriebsprozess, der nicht unerhebliche Risiken mit sich bringt und der in vielen verschiedenen Betriebsarten vorkommen kann. Neben eigenständigen Standorten (meistens kleine bis mittelgroße Unternehmen mit Versicherungssummen zwischen USD 10 Mio. und USD 100 Mio.) finden sich Galvanisieranlagen als Nebenbetrieb in einer Vielzahl von Produktionsbetrieben.
Laut den Ergebnissen einer GDV-Arbeitsgruppe sind Schäden in Galvanikbetrieben tendenziell eher groß. Als Hauptursache werden häufig durch Korrosion und mangelnde Instandhaltung und Wartung defekte Heiz- und Elektroinstallationen festgestellt. Präventive Maßnahmen – beispielsweise Sprinkleranlagen, nicht brennbare Baumaterialien, automatische Feueralarmsysteme, räumliche/bauliche Komplex- und Brandabschnittstrennungen für den Galvanisierungsbetrieb sowie regelmäßige Wartung und Instandhaltung – können die Wahrscheinlichkeit einer Brandentstehung oder zumindest die Brandschadenfolgen verringern.
Insbesondere rücken zunehmend Betriebsunterbrechungsschäden bei Galvanikbetrieben in den Vordergrund, da die Wiederaufbauzeit und die Herstellung der vollen Produktionsfähigkeit bis zu 24 Monate dauern kann. In dieser Zeit ist auch damit zu rechnen, dass Kunden aufgrund fehlender Ausweichmöglichkeiten nicht beliefert werden können und möglicherweise zu einem Mitbewerber wechseln.
Demzufolge kann das Underwriting bei Galvanisierungsunternehmen komplexer sein als erwartet. Um auch in der Zukunft die Versicherbarkeit zu angemessenen Versicherungsprämien zu sichern, sollte den möglichen Risiken bei einem Galvanikbetrieb, insbesondere zu erwartender Betriebsunterbrechungsrisiken, besondere Aufmerksamkeit gewidmet werden.
Zur Ansicht der Checkliste/Empfohlene Brandschutzmaßnahmen, der Literaturhinweise und Endnoten öffnen Sie bitte die PDF-Datei.