More and more frequently at conferences and in the media, we are hearing about the erection of wood-based buildings and high-rises. Thanks to advances in wood-engineered products and fabrication, tall timber buildings can have the same, if not better structural integrity than buildings erected with steel and concrete.
People already speak about the end of steel and concrete as the predominant construction material. Wood is promoted to be the material of the future, as wood structures can be erected faster at significantly lower cost. They are also considerably lighter and more environmentally sustainable than their concrete counterparts.
As a consequence, more and more buildings around the world are springing up, using engineered wood materials, elements and/or components. And they are getting taller. For example, 9 to 18 storey buildings have already been built in Austria, Australia and in the UK. In Sweden and in the UK plans are in place for buildings of between 40 and 80 storeys high, and more will follow.
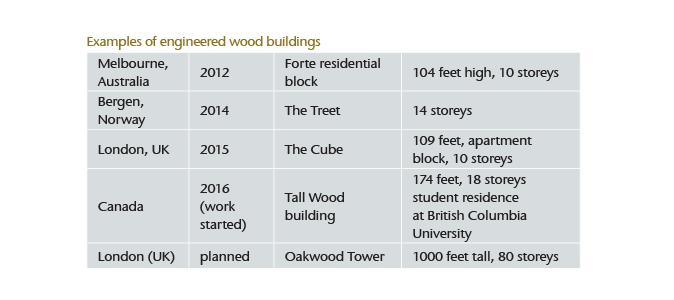
This article discusses these “new” construction materials, alongside some important underwriting considerations.
What is engineered wood?
Engineered wood (also called composite wood, man-made wood or manufactured board) includes wood products that are manufactured by binding or fixing strands, particles, fibers, veneers or boards of wood with adhesives or other methods in order to form composite materials. These production processes can overcome natural variations in the wood, resulting in composite panels that consistently meet the structural, thermal, acoustic and fire safety criteria for use in conventional construction.
Of the various engineered products available, the most common are:
CLT – Cross-laminated timber
CLT panels are (usually) made from three to seven layers of boards stacked crosswise and secured with glue, fasteners or interlocking dovetails. Up to 10 layers can be glued together in a press. Even low-grade woods like spruce are capable of supporting tremendous loads. In the event of a fire, CLT panels are engineered to produce a blackened char that resists further burning. They are mainly used for building and roof frameworks, predominantly for roof girders, and more rarely for supporters.
Glulam – Glue-laminated lumber
To make glulam, smaller pieces of wood are stuck together to create structural members with greater tensile strength than steel and better compression than concrete. Sometimes it is used as a direct replacement for steel and concrete members.
LVL – Laminated veneer lumber
To produce LVL, layers of wood veneers are laminated together using an adhesive and cured in a hot press. The grain of the wood runs parallel to the long end of the panel. Similar to plywood but much larger in scale, LVL is used in a variety of applications, including beams, joists, trusses, frames, roof, floor and wall elements, and components for the joinery industry (doors, stairs, windows).
LSL – Laminated strand lumber
A structural composite, LSL is manufactured from strands of wood blended with an adhesive. Strands are oriented parallel to the length of the beam and then compressed using a steam injection press. It is made from cheap flakes and chips of wood.
SIPS – Structural Insulated Panel Systems
SIPS consist of two timber panels of Oriented Strand Board (OSB) and an internal layer of Expanded Polystyrene (EPS). It is used for insulation and building acoustics.
Plywood
In order to produce plywood, thin layers or “plies” of wood veneer are glued together with the grain of adjacent layers rotated up to 90 degrees.
MDF – Medium-density fiberboard
MDF panels can be fabricated by combining wood fibers with wax and a resin binder; panels are formed by applying high temperature and pressure.
Particle board
Particle board or chipboard is produced from wood chips, sawmill shavings or sawdust that are combined with a resin binder and then pressed and extruded.
OSB – Oriented strand board
Also known as flake board, wafer board, or chipboard, OSB is similar to particle board but uses machined wood flakes, offering more strength.
What’s so good about wood?
As a construction material, engineered wood has some impressive attributes that explain its increasing popularity with the construction industry, architects and politicians. These include:
- Wooden buildings are significantly lighter and show a similar or even better structural integrity than steel or concrete buildings.
- Wood is a natural, renewable material that meets current “green” goals in saving energy and reducing the production of carbon dioxide emissions.
- The greater strength and design flexibility of engineered wood are inspiring ever greater ambitions in architectural and structural design.
- Wood allows the pre-fabrication of parts, components and construction elements, which reduces the costs of shipping and assembly at the construction site.
- Effective fire resistance can be achieved using thick, heavy and cross-laminated timber or by covering the wood with a layer of drywall.
- Wood forms a char layer when it burns, protecting the inner wood underneath. This increases the duration before a building collapses in the event of a fire, giving people more time to escape and fire departments a better chance to fight the blaze.
Why must property insurers apply caution?
Despite some clear benefits, the growing number – and sheer size – of buildings being constructed from engineered wood is a source of concern for insurers. These mainly stem from the natural behaviour of wood when exposed to fire, water or moisture but are intensified by legislators seemingly supporting a lowering of safety standards in the pursuit of greener construction.
As recent fire losses in the U.S. on large wooden apartment and condominium buildings show, wood-based buildings inherently represent a high fire load with the tendency to burn to the ground if the fire is not quickly detected and extinguished.1
Even when a fire is successfully extinguished before a building is damaged to the point of needing to be demolished, the wood could have been burned to some degree. There is no guarantee that the supporting structure will remain as safe as planned in the original construction, even with restoration. Of course, it is possible to apply chemicals to wood in order to lower ignitibility and combustibility, but these are often not used due to fears they could be harmful to people.
Just as steel and concrete buildings need additional insulation to be energy efficient, so do those made from engineered wood. To meet required energy-saving standards, they are often insulated with combustible materials (such as polystyrene, polyurethane, straw or other dried natural fibers and grains). Fire fighters cannot effectively fight a fire that is spreading inside the wooden walls, ceilings and insulation material; they can only try to prevent a fire from spreading over to the next building. As a result the affected building burns completely.
Water used in extinguishing the fire can also prove problematic, penetrating the wood and leading to additional consequential losses. As a rule, wood-based materials and components don’t respond well to moisture and humidity. The experience of insuring wood-based construction shows significantly higher building losses after a pipe leak. Water damage tends to spread more rapidly and remain undetected longer than in concrete structures; it can affect the safety of the whole structure or can even make it uninhabitable due to extensive rot and mold. The consequential losses often mean the building cannot be repaired and needs to be taken down.
Because of cladding and decorations, it can be very tricky for a fire or insurance surveyor to identify wood materials in buildings or the insulation material that was used. In some cases wood components appear to consist of solid wood; however, if someone were to cut through a girder, it would become apparent that this is not the case. Some structures only look like they are made from solid cross-laminated timbers, where in actual fact engineered wood has been used to save money on materials. These factors make it difficult to classify wooden buildings correctly.
Finally, occurred losses already indicate that in terms of loss expectancies, wooden buildings of whatever construction and dimension have a higher tendency to become a total loss and therefore the maximum foreseeable loss results in a 100% estimate.
For these reasons, wooden buildings should not simply be viewed as being more ecological and economical; their vulnerability and exposure to fire and moisture losses need to be considered as well. Preventative measures – such as sprinkler installations and automatic fire and water leakage detection systems – must be installed to safeguard the advantages of wood-based construction, combined with a safety standard at least equivalent to that used in standard building constructions.
Summary
In the global trend toward the construction of buildings that meet ecological needs, wood has some clear advantages over traditional construction materials such as steel and concrete. With advances in engineered wood materials and components come possibilities to construct increasingly larger buildings – a trend being witnessed around the world.
This poses challenges not only for fire departments but also for underwriters tasked with evaluating such buildings according to their inherent exposures. Some of these implications can and should be minimized by precautionary safety measures, but it is essential that insurers have a thorough grasp of the risks involved.
If you are interested in deepening your understanding, we would be happy to share our knowledge of this topic with you. Don’t hesitate to get in touch.
Download PDF version for Further Reading